Main cost drivers in injection moulding and actionable design tips
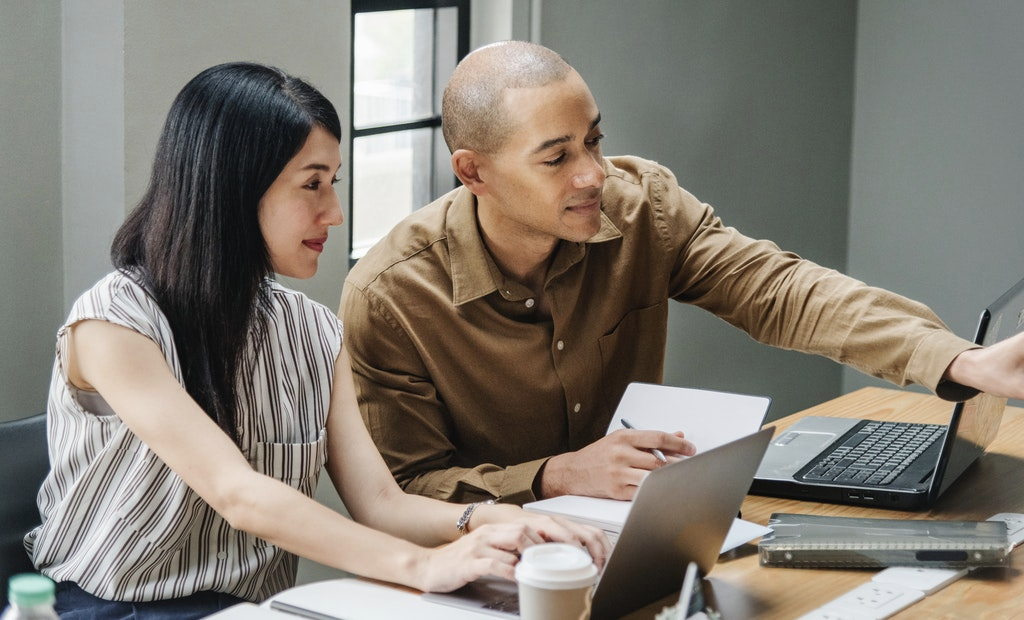
The advanced technology of injection molding services is fast becoming the preferred choice of many forward-thinking plastic product manufacturers. Many appreciate that a large number of fast runs from start to finish are cost economical and efficient. Even so, there are cost drivers that can raise manufacturing expenses if careful consideration isn’t given to the creation process prior to approving the start of production. Find out what key aspects push up costs, and how to address them while still maintaining product quality.
Cost raising factors in Injection moulding
The tooling expense
Custom moulds, by their very nature, are pricey and each one can cost as much as $100,000. On the low end, approximately $5,000 is the minimum expense for a very small, simple mould. Because of the cost of tooling, larger productions with unit orders of more than 500 make injection moulding feasible and worthwhile.
Design modifications
Changes in mould design after it has been created drive up the cost. Typically, the original mould can’t be adjusted, so an entirely new mould must be created. Mould revisions at least double the price of the mould because of retooling.
Tips on how to lower the cost of injection moulding
Tip #1: Use the straight-pull mould
The basic mould called the straight-pull mould costs the least. It contains only two parts:
- Core – It’s considered the A-side, and it’s nearest to the injection unit that focuses on the appearance of the finished part.
- Cavity – It’s referred to as the B-side. The backside of the mould holds the structural elements like bosses, ribs, and snap-fit joints to aid in creating the mold. Ejector pins push the part out of the mould after the cavity cools too.
Other moulds, such as those that contain a side-action core, raise the tooling costs to about $1,500 and sometimes as much as 30 per cent.
Tip #2: Use one mould for multiple parts
It’s common to include up to eight parts of the same type into one mould. A production time savings of 80 per cent is often brought about with this approach. The mould design can feature interlocks with hinges or location points within the mould to create a minimum of two pieces at once.
Tip #3: Trim the wall thickness
Just a small millimetre reduction in wall thickness saves cycle time by as much as 75 per cent, and at the very least 50 per cent. This is due to the solidification of thinner parts which occurs more quickly. Take care not overly thin out the walls. If this happens, the quality will suffer. The good news is that ribs placed in certain areas within the mould increase a part’s wall thickness without degrading the performance of the moulding system.
The cost drivers of injection moulding are best managed effectively with pre-planning and reviewing the mould design prior to manufacturing can save your firm thousands of dollars. Using simple moulds that fit more than one part reduces cycle time and lowers production costs as well. Finally, a part’s wall thickness matters because thinner walls make for a speedier part solidification process.
Manufacturing firms can now take advantage of the technology that injection molding offers. Get started by requesting an instant injection moulding quote today. Keep in mind, instant quotes are available for sheet metal fabrication services too. After you realize the savings, you’ll want to save even more on all of your production needs.
The editorial unit
Facebook
Twitter
Instagram
YouTube
RSS