Effective process-cooling tips to reduce energy costs
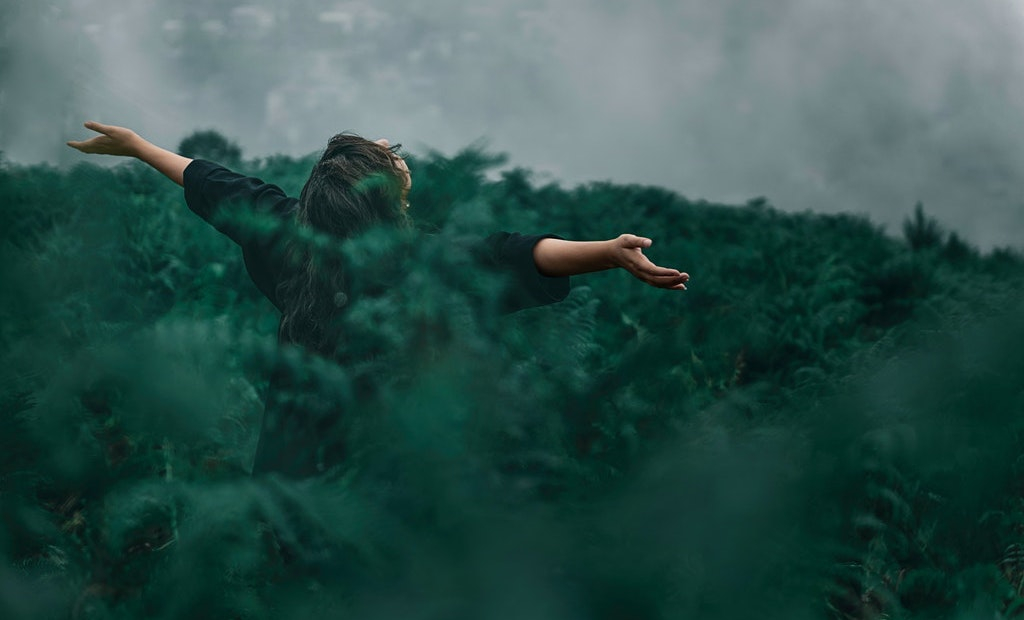
According to the stats, the biggest chunk of site costs is associated with refrigeration. In particular, cooling the foods, drinks, chemicals, and pharmaceutical processes account for up to 90 per cent of energy costs. These costs can be overwhelming. However, you can take certain measures to minimise these costs; according to experts, you don’t have to employ expensive measures to do so. All you need is to adopt the following strategies and you could end up cutting 20 per cent of energy costs in your refrigeration plant.
The basics: Process cooling
By definition, process cooling is actually a chiller that utilises mechanical refrigeration when it comes to removing excess heat from an engineering process. You can use chillers in a myriad of applications. From food processing to medical imaging, chillers are important in any process. You can use chillers in printing, medical engineering equipment, packaging, and even food processing. Chillers remove excess heat from a process, which optimises the performance of the equipment involved. Also, the use of chillers improves the quality of output. Even more, chillers help equipment last longer. So, don’t let excess heat pin you down. You can remove it effectively and improve efficiency as well as performance. All you need is to choose the best chiller. Evaluate your requirements. Look at your budget. Learn how a chiller works. Ask for referrals. Look at the testimonials. Ensure that you get a warranty.
Properly maintaining your chilled system
Maintenance is a key aspect when it comes to cutting down on energy costs. Poorly maintained systems tend to be inefficient. This leads to high energy costs. So, work on the maintenance aspect of your chilled system. Clean it properly. Clean the tubes. Alternatively, you can hire the services of an expert to help you maintain your chiller system.
Plan on how to conduct preventative maintenance. It will mitigate the risks that are associated with downtime. It’s also important to note that a frequently used system should be cleaned on a regular basis. How often you will carry out maintenance will depend on how you use your unit.
Water quality inspections and treatment
Don’t feed any water into your chiller. It might end up corroding the loop system and lead to inefficiencies. Instead, consider treating any water that goes into your chiller. Use high-quality glycol to protect the pipes from freezing, corrosion, as well as bacteria. You can take water samples to water engineers for PH tests. It will give you a clear picture concerning the quality of your water. With this strategy, you would have shielded yourself with costs that are normally associated with replacing the whole equipment.
High-efficiency and eco-design models
Chiller lifespan is highly dependent on how often it’s used and maintained. For instance, manufacturing chillers are used more than their comfort creating counterparts. So, when looking for a chiller for manufacturing processes, consider going for a highly efficient one. A highly efficient chiller will save you a lot of money in terms of energy costs. Plus, the maintenance costs of a highly efficient chiller are lower. Even more, they last longer. Also, consider going for an eco-design chiller for compliance purposes. Remember, the world is going green. Engineers are looking for eco-friendly solutions. So, invest in a chiller that is eco-friendly.
External installation and free cooling coil
Capitalise on free cooling when the winter and autumn seasons approach. Taking your chiller outside and utilising fee cooling can save you up to 70 per cent of energy costs.
Replacing the cooling towers
Cooling towers can be expensive to run and maintain. They can also waste a lot of water. Thus, they need a legionella risk assessment. This is because they use a lot of water. Thus, consider replacing the cooling towers. It will save you a lot of money in terms of energy costs. Even more, it will reduce health and safety-related risks.
Using adiabatic fluid coolers
It’s important to note that any plastic processing facility has a cooling tower that offers to cool the hydraulics, chiller condensers, as well as other equipment. Any cooling tower is equipped with a fan that evaporates water, leading to the production of an 85°F process water. Of course, it offers effective cooling. However, this technique ends up consuming huge amounts of water. Even more, it requires water treatment so that it can control biological growth. Remember, cooling towers tend to expose your process water to the environment/atmosphere. Consequently, you will be requiring constant filtration. On the other hand, fluid coolers tend to use less water. Even more, they rely on ambient temperature from the air. This makes them an ideal solution – especially when it comes to looking for energy-saving cooling solutions. Additionally, adiabatic fluid coolers utilise evaporative pads when expanding an effective temp range. By doing so, the water usage is significantly reduced. So, instead of cooling towers, go for fluid coolers.
Variable-speed based chiller compressors
Use variable-speed chiller based compressors. They are effective in reducing energy consumption. Remember, processing plastics require water that’s cooler than the level of 85°F. In this case, a chiller does an excellent job. According to experts, a chiller is equipped with a refrigerator, compressor, as well as an evaporator. It uses these three components to remove heat from any process. This can result in a fluid process temperature of about 50°F or so. Of course, compressors and refrigerators aren’t new in this industry. They have been used since the 19th century. However, most of them relied on a fixed speed. However, technology is now changing. With the introduction of variable speed compressors, you have control over many parameters. This helps reduce energy consumption. You can slow down the compressor’s speed depending on the needs and conditions. Thus, you don’t have to waste any energy.
The bottom line
Tired of ever-increasing energy costs? Well, worry no more. The above are the tips you need to significantly cut down on these costs as far as your home’s cooling system is concerned. From properly maintaining your chilled system to using variable-speed chiller based compressors – these are the tips from experts. They will help you deal with those escalating energy costs once and for all.
The editorial unit
Facebook
Twitter
Instagram
YouTube
RSS